Smart Factories and Digital Twins: How Global Giants Use AI to Simulate and Optimize Production
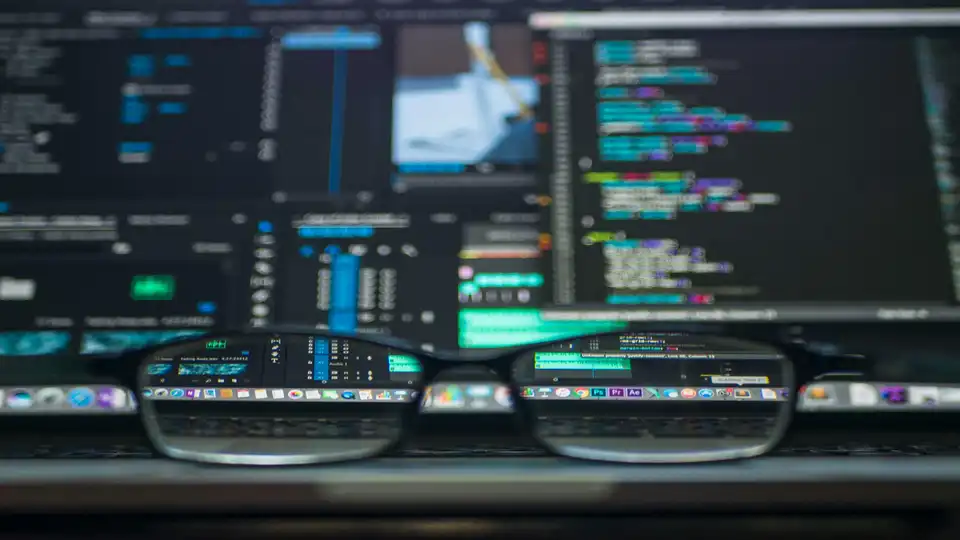
In today's fiercely competitive global manufacturing world, smart factories and digital twin technology are quickly becoming crucial strategic advantages that industry giants are all scrambling to grab. These technologies aren't just completely transforming traditional production methods; they're also bringing unprecedented boosts in efficiency and major cost savings to businesses.1 This article will dive into how leading global companies are completely reshaping their production processes using AI-powered digital twin technology, achieving full-spectrum optimization from initial design all the way through to manufacturing.
Digital Twin Technology: A Manufacturing Revolution That Blends Virtual and Real
At its core, a digital twin is essentially a virtual replica of a physical object or system existing in the digital realm.2 This concept actually started with NASA, who used it for remote monitoring and simulating spacecraft.3 Now, it's being widely applied in manufacturing. In a smart factory setup, digital twin technology plays several key roles:
- It creates a real-time map of how physical equipment is performing and its operational status.4
- It lets you simulate production scenarios and predict potential problems before they happen.5
- It helps optimize production processes and how resources are allocated.6
- It provides crucial support for remote monitoring and decision-making.7
According to Gartner's predictions, by 2025, over 70% of manufacturers will have deployed digital twin technology—that's double the 35% seen in 2021. This data really highlights just how much the market is embracing this technology and its massive growth potential.
Siemens: A True Pioneer of Digital Twins
German industrial giant Siemens isn't just an early adopter; they're a true industry benchmark for digital twin technology.8 Siemens' digital twin strategy spans three crucial dimensions: product, production, and performance, forming a complete, closed-loop system.9
The Amberg Factory: A Digital Twin Masterclass
Siemens' electronics factory in Amberg, Germany, is widely considered a prime example of "Industry 4.0."10 This factory achieves seamless digital integration of both product and production thanks to digital twin technology:
- Every single production line and every piece of equipment has its own corresponding digital twin.
- Changes to product design can be quickly tested and validated for feasibility in a virtual environment.11
- Any optimization to the production process is first simulated and validated within the digital twin.12
- AI algorithms are constantly analyzing operational data, predicting equipment performance, and fine-tuning maintenance schedules.13
Data shows that the Amberg factory has achieved remarkable results through its digital twin implementation:
- Product time to market cut by 50%.
- Engineering design efficiency boosted by 30%.
- Production flexibility increased by 20%, allowing it to simultaneously produce over 1000 different products.
- Production quality improved by 15%, with defect rates slashed to parts per million.
Siemens' Chief Digital Officer once remarked, "The digital twin isn't just a technical tool; it's the core engine of our enterprise's digital transformation. It fundamentally changes how we design, manufacture, and maintain products."14
GE: Digital Twins for Smarter Wind Farms
General Electric's (GE) application of digital twin technology in wind power generation is another fascinating case study. GE's wind farm digital twin system can simulate the operational status of an entire wind farm, including individual wind turbine performance parameters, environmental factors impacting the farm, and grid connection conditions.15
Data-Driven Performance Optimization
GE's wind farm digital twin system crunches over 400GB of data daily, with AI algorithms analyzing this massive dataset to:
- Predict how weather changes will affect power generation.
- Adjust wind turbine blade angles in real-time based on wind direction and force.
- Identify potential failures and schedule preventive maintenance proactively.16
- Optimize the overall energy output of the entire wind farm.17
In a large-scale wind farm project located in Texas, USA, this system helped the operator achieve some impressive results:
- Overall power generation increased by 8%.
- Maintenance costs reduced by 20%.
- Wind turbine lifespan extended by 15%.
- Operating downtime reduced by 40%.
GE's Chief Technology Officer of Wind Power stated, "Digital twin technology lets us test various 'what-if' scenarios in a virtual environment and pinpoint the best operating parameters, which was simply unimaginable before."18
Tesla: Real-Time Production Line Optimization
Tesla deeply integrates digital twin technology with AI to create a highly automated smart factory system.19 The "Production Line Digital Twin" system at Tesla's Fremont factory is a central pillar of its "Robot Manufacturing Robot" strategy.
Production Lines That Adjust in Real-Time
Tesla's production line digital twin boasts several key characteristics:
- Each production line is packed with thousands of sensors that collect production data in real-time.20
- The AI system analyzes these data streams to pinpoint production bottlenecks and potential quality issues.
- Digital models can predict how different production parameters will impact product quality.21
- The system can automatically adjust production parameters on the fly to achieve dynamic balance across the production line.
According to Tesla's 2023 investor report, their digital twin system has yielded significant benefits:
- Model Y production line efficiency boosted by approximately 40%.
- Production line reconfiguration time slashed from weeks to days.
- Maintenance plan optimization cut downtime by roughly 30%.
- Defect rates reduced by 23% through predictive quality control.
Tesla's Chief Engineer once noted at a tech summit, "Our factory isn't just a place to build cars; it's a massive learning system. Digital twin allows our factory to learn from its own experiences and continuously optimize its production processes."22
P&G: A Digital Revolution in Consumer Goods Manufacturing
Procter & Gamble (P&G) is applying digital twin technology to its fast-moving consumer goods production lines, creating a system they call "The Digital Engine."23 This is a fantastic example of digital transformation in traditional manufacturing.
A Digital Backbone for Flexible Production
P&G's digital twin system covers the entire process, from raw materials all the way to finished products:
- It simulates the production feasibility of different formulas and packaging options.
- It predicts production line changeover times and associated costs.
- It optimizes scheduling strategies for producing multiple product variations (SKUs).
- It provides real-time monitoring of product quality and production efficiency.
P&G operates over 100 factories worldwide, and their digital twin strategy has been implemented in 70% of them. A classic success story comes from their home care products factory in California, which achieved the following thanks to digital twin technology:
- New product time to market reduced by 35%.
- Production line utilization rate increased by 23%.
- Product changeover time cut by 50%.24
- Energy consumption reduced by 17%.
P&G's Chief Supply Chain Officer highlighted in their 2023 annual report, "Digital twin technology has completely changed our production methods. It empowers us to quickly react to shifts in market demand while maintaining optimal operational efficiency."25
Bosch: A Cross-Factory Digital Twin Network
German industrial powerhouse Bosch has built an impressive cross-factory digital twin network, linking over 240 factories globally. This creates a true "Global Smart Manufacturing Network."
Shared Knowledge and Collaborative Optimization
Bosch's digital twin network doesn't just replicate individual factory operations; it also establishes a powerful cross-factory knowledge-sharing mechanism:
- Production data from various factories is centrally analyzed to identify best practices.
- Process improvements made in one factory can be rapidly rolled out to others through their digital twins.
- The AI system can compare performance indicators across different factories and recommend improvement plans.
- Global supply chain optimization is collaboratively simulated using digital twins from multiple factories.
In an experiment conducted between two similar factories in Germany and China, Bosch achieved impressive results using digital twin technology:
- Production efficiency increased by 18%.
- Quality consistency improved by 12%.
- Energy consumption reduced by 15%.
- The time it took to roll out new processes globally was slashed from an average of 6 months to just 6 weeks.
Bosch's Senior Vice President of Manufacturing Technology stated, "Digital twin enables us to break geographical limitations and quickly replicate global best practices to every production base. This is the cornerstone of our digital transformation strategy."
The Technical Architecture of Digital Twins
To create a fully functional digital twin system, you need a sophisticated, multi-layered technical architecture:
Perception Layer
This layer is all about collecting data from the physical world. It typically includes:
- Industrial Internet of Things (IIoT) sensor networks.
- Machine vision systems.
- RFID and barcode scanning systems.
- Operator input terminals.
According to IDC statistics, by the end of 2023, the number of global industrial IoT connected devices topped 12 billion, with approximately 40% of those specifically supporting digital twin applications.
Data Processing Layer
This layer is responsible for processing and integrating the massive amounts of data flowing in from the perception layer:
- Edge computing systems for real-time data crunching.
- Cloud platforms for massive data storage and analysis.26
- Data cleaning and standardization tools.
- Time-series databases and data lakes.
Model Layer
This is the very core of the digital twin, encompassing:
- Physical models: Simulations based on fundamental laws of physics.
- Statistical models: Predictions drawn from historical data.
- AI models: Uncovering complex relationships through machine learning.
- Hybrid models: Comprehensive models that combine the above methods for a holistic view.
Visualization and Interaction Layer
This layer is all about presenting digital twins to users in an understandable way:
- 3D visualization platforms.
- AR/VR interaction systems.
- Mobile applications.
- Consoles and dashboards.
Implementation Challenges and Solutions
Despite the immense promise of digital twin technology, there are still several significant hurdles in the implementation process:
Data Quality and Compatibility
Problem: Data formats and qualities generated by different devices, especially from different eras, vary wildly, making integration a real headache.
Solutions:
- Deploy edge gateways to standardize data formats and communication protocols.
- Use AI-assisted data cleaning and validation tools.
- Establish unified data standards and industrial semantic models.27
- Implement robust data quality assurance processes.
General Electric's "Predix" platform successfully tackled the data standardization problem using its "Digital Twin Blueprint" framework, allowing seamless integration of data from devices of vastly different ages.
Model Accuracy and Computational Efficiency
Problem: High-precision models demand enormous computing resources, but industrial environments often require real-time responses.28
Solutions:
- Adopt a multi-precision model strategy, choosing the appropriate level of precision for different needs.
- Utilize edge computing for real-time needs and cloud computing for more complex analysis.29
- Employ model compression and optimization techniques.
- Develop adaptive sampling strategies to reduce the volume of data needing processing.
Siemens' "Mindsphere" platform uses "dynamic precision adjustment" technology to reduce the computational load for non-critical parameters while keeping key parameters highly accurate.
Security and Privacy Protection
Problem: Digital twins contain core production data, making them high-value targets for security risks.30
Solutions:
- Implement multi-layered security protection strategies.
- Use robust data encryption and access control technologies.
- Establish strong security audit and monitoring mechanisms.
- Develop data anonymization and de-sensitization tools.
The "Secure Digital Twin Architecture" developed by Bosch utilizes blockchain technology to ensure secure data exchange while enabling controlled knowledge sharing between different factories.
Future Outlook: The Evolution of Digital Twins
Digital twin technology is rapidly evolving towards an even more intelligent and autonomous future:
Autonomous Digital Twins
Future digital twins will have much greater autonomy:
- They'll be able to adjust production parameters on their own for optimal operation.31
- They'll proactively identify optimization opportunities and suggest improvements.32
- They'll handle routine decisions without human intervention.33
- They'll continuously improve their own models through reinforcement learning.
Cross-Domain Integrated Digital Twins
Digital twins will break free from single-field limitations:
- They'll integrate product, production, and supply chain digital twins.
- They'll interconnect with external digital twins, like those for cities and energy grids.
- This will lead to the formation of much larger-scale digital ecosystems.
- They'll support more comprehensive optimization decisions across entire value chains.34
Human-Machine Collaborative Smart Factories
Digital twins will become the essential link for collaboration between humans and intelligent systems:
- They'll enable intuitive human-machine interaction through AR/VR.35
- They'll support collaboration between remote experts and local operators.
- They'll provide context-based intelligent decision support.
- They'll empower workers to become the central figures in the digital factory.
Conclusion
Digital twin technology is fundamentally reshaping the global manufacturing landscape.36 From Siemens and GE to Tesla and P&G, industry giants are leveraging this technology to build new competitive advantages.37 For manufacturing companies, digital twins aren't just a technical tool; they're a strategic asset. They're poised to become the nerve center of future smart factories, pushing production systems toward greater efficiency, flexibility, and sustainability.38
With AI technology constantly advancing and the Industrial Internet of Things becoming more widespread, there's every reason to believe that digital twins will transform from a distinguishing feature of advanced manufacturing companies into an industry standard and basic capability within the next decade. Companies need to recognize the strategic value of digital twins and embrace them as a core tool for digital transformation to truly build smart manufacturing capabilities.
References
- Gartner. (2023). "Predicts 2024: Digital Twins Will Transform Manufacturing Operations."
- McKinsey & Company. (2023). "Digital Twins: The Foundation of Smart Manufacturing."
- Siemens AG. (2023). "Digital Enterprise: The Comprehensive Digital Twin."
- GE Digital. (2023). "Digital Twin: Bringing the Physical and Digital Worlds Together."
- Tesla, Inc. (2023). "Manufacturing Efficiency Report 2023."
- Procter & Gamble. (2023). "Annual Report: Digital Transformation in Manufacturing."
- Bosch. (2023). "Connected Manufacturing: Global Factory Network."
- IDC. (2023). "Worldwide Internet of Things Spending Guide."